Case Studies
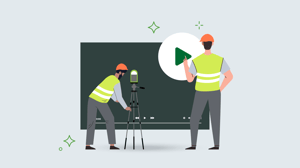
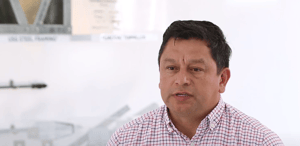
USG LATAM is reshaping the construction industry across residential, commercial and industrial sectors in Latin America.
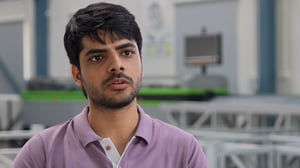
S2S Designs has over a decade of experience using LGSF to construct walls and roofs for industrial, residential, and commercial sectors across India.
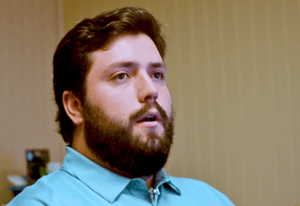
US-based Accurate Steel Fab manufactures pre-panelized steel components for residential and commercial sectors across Texas.
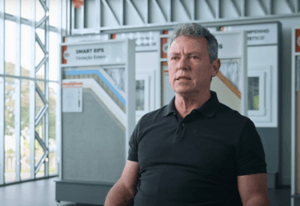
Espaço Smart is pioneering the Brazilian construction industry with steel framing. It is the first retail store in Brazil to allow customers to purchase homes or commercial buildings directly from the store.
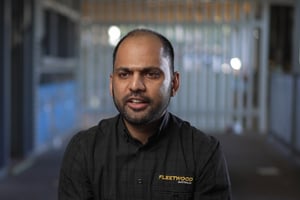
Fleetwood Australia has been in the construction business for 60 years. They are using steel framing to produce wall, roof and ceiling frames for their modular buildings.
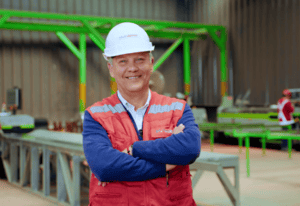
MultiAceros is a manufacturing company specializing in cold-formed steel that focuses on detailing, engineering, and supplying lightweight construction systems throughout Chile.
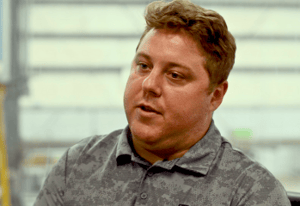
Intellistructure specializes in supplying steel framing and components for residential constructions across Florida and the entire US East Coast, an area that is prevalent for its high winds and hurricanes.
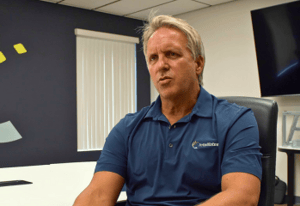
Intellisteel specializes in the design and manufacture of cold formed steel framing, offering a comprehensive range of services that extend from turnkey modular solutions to off-site and on-site applications throughout the United States.
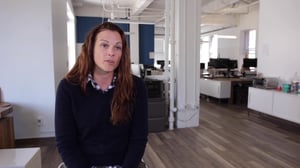
ICS engineers, designs and manufactures prefabricated buildings across the US and specializes in multi-site deliveries.
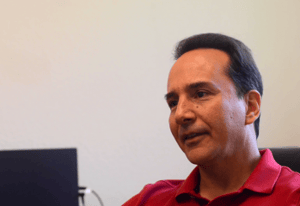
US-based Orlando Steel Framing sees time-saving as one of the biggest advantages of cold formed steel framing.
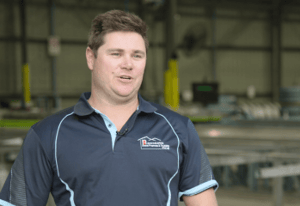
Over the past decade, Newcastle Steel Frames & Trusses have been supplying steel framing to their loyal customer base in both residential and commercial construction projects across NSW.
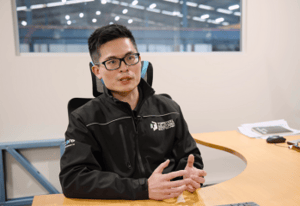
Topsteel Solutions have been providing residential and commercial customers with LGS framing for the last 8 years across New South Wales, Australia.
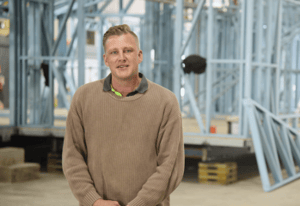
Sydney based Manor Homes have been in the residential construction business for 30 years, originally working with timber. Their business is now focused on transportable homes using steel framing.
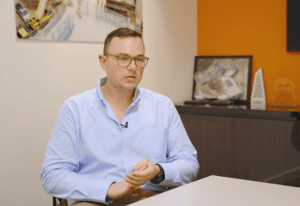
Sydney based, Austruss sees speed and cost as the biggest benefits of LGS framing.
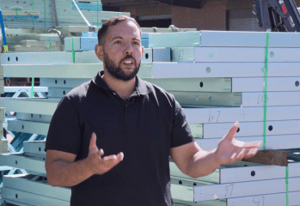
Sydney Frames & Trusses find the versatility that the FRAMECAD system offers a huge advantage.
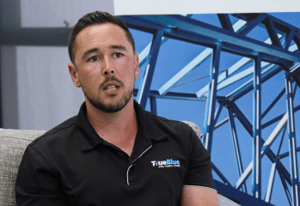
Sydney, Australia based True Blue Steel Frames see many benefits of building with steel frames, straightness is just one of them.
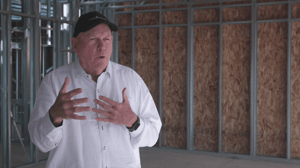
Do-it-yourselfers are buying steel framing house kits from U.S. based Frame Up Now and constructing their own house framing onsite.